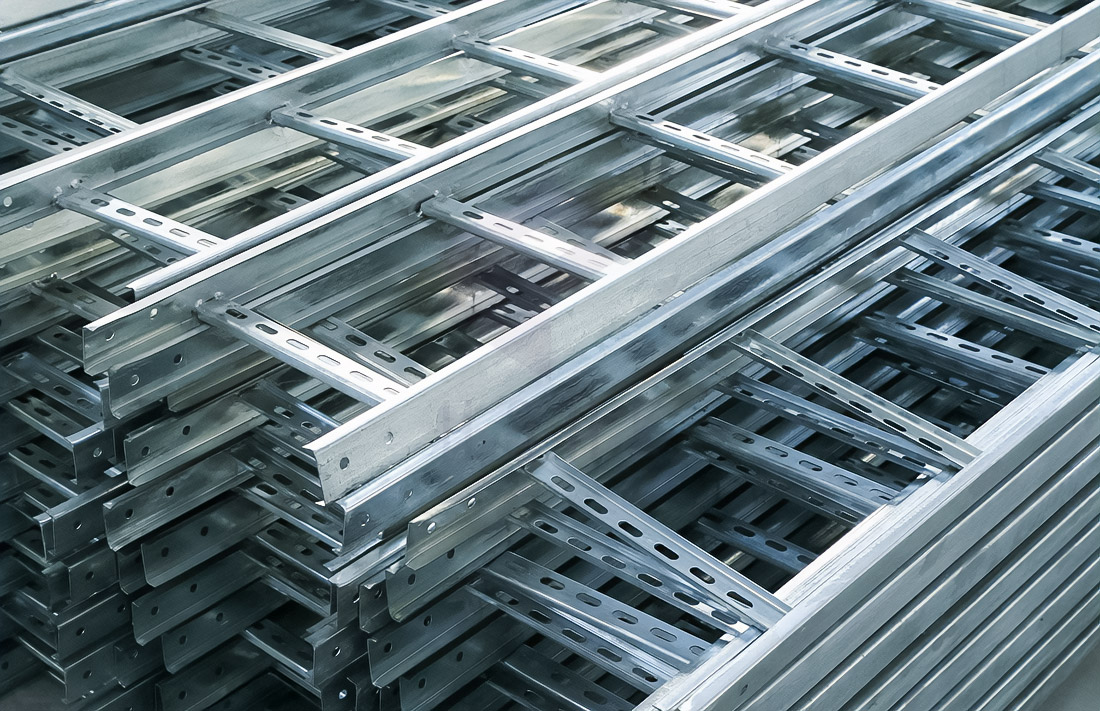
Corrosion-Resistant Innovations: Progress in Protection of Cable Systems
Cable trays and their accessories — this important elements modern cable systems, providing reliable and organized laying wires and cables in buildings and industrial facilities. Trays manufactured from various materials, including steel, aluminum and plastic, and can be presented in form ladder, perforated or solid structures. Accessories, such as connecting elements, fasteners and plugs, play key role in providing integrity and functionality system. Important aspect is choice correct wire mesh cable tray manufacturer, which guarantees quality and reliability products.
Historically proven significance, cable trays first appeared in 1950s, but quickly became basis for laying cables. For example, in one of large companies, applied this method, mechanical damage cables was reduced by 30%. However, despite their significance, cable trays and their components often subject to corrosion. This caused by exposure aggressive factors, such as humidity, chemicals and extreme temperatures, what particularly relevant in industrial and marine conditions. Corrosion capable cause reduction mechanical strength, deterioration electrical insulation and, ultimately, failure system.
Importance corrosion-resistant coatings: More, than just Protection
Corrosion-resistant coatings play critical role in protection cable trays and their accessories from destructive impact environment. These coatings not only extend service life equipment, but and significantly reduce costs for maintenance and replacement. Use protective coatings allows preserve aesthetic appearance structures and ensure their reliability and safety throughout entire service life.
One of studies showed, that use such coatings extends service life cable systems on average by 50%, what can mean savings in millions dollars for large industrial facilities. Coating also contributes to maintaining aesthetic appearance, what important in corporate and public spaces.
Types corrosion-resistant coatings: Variety and Characteristics
Exists many types coatings, providing protection from corrosion. Consider most common of them:
-
Galvanization
- Description: Process coating metal surface layer zinc for preventing corrosion.
- Advantages: High resistance to corrosion, especially in conditions exposure moisture and salt. Durability and low cost.
- Disadvantages: Limited effectiveness in aggressive chemical environments. Possibility mechanical damage coating. In Shipbuilding company N, where operated such coatings, periodically occurred chips and cracks, requiring repairs, what increased expenses by 10% annually.
-
Powder coatings
- Description: Method application dry powder material with subsequent heating for forming strong and uniform coating.
- Advantages: High resistance to mechanical damage and chemical substances. Wide choice colors and textures allows aesthetically adapt equipment in integrated systems.
- Disadvantages: Requires special equipment for application. Limited resistance in conditions extreme temperatures. In company M coating withstood temperatures up to 150°C, what suited for their high-temperature processes.
-
Epoxy resins
- Description: Two-component systems, forming strong and chemically resistant coating.
- Advantages: Excellent adhesion to various materials, high chemical resistance and durability. Application in company S reduced costs by 15%, thanks to long service life coating. More about epoxy coatings.
- Disadvantages: Sensitivity to ultraviolet radiation, what can cause discoloration and cracking after 5-7 years operation on open air.
Application coatings in various conditions: Point Recommendations
Different types coatings find their application in diverse industrial conditions. For example, in marine environment, where increased humidity and content salt in air, most effective considered galvanized coatings. In chemical industry, where equipment exposed to aggressive chemical substances, epoxy resins show their best qualities. Powder coatings often used in conditions, where required high mechanical strength and aesthetic attractiveness.
One of successful applications was recorded in marine docks company X, where galvanization reduced corrosion by 70%. In chemical company Y use epoxy resins increased reliability equipment by 25% in aggressive environments.
Modern research and innovations: Path in Future
Modern research in field corrosion-resistant coatings aimed at development new materials and technologies, providing even more high resistance in aggressive conditions. Promising direction is application nanomaterials, such as graphene, which can significantly improve protective properties traditional coatings. In course research at University Z graphene coatings showed improvement resistance to corrosion by 85%.
Also studied biocompatible and environmentally friendly coatings, what especially important in conditions growing attention to questions ecology and sustainable development. In company A application such coatings allowed reduce impact on environment by 40%. Environmental coatings and their advantages.
Future trends and prospects: Vision Tomorrow Day
With development technologies and tightening requirements to reliability and durability cable systems expected further improvement corrosion-resistant coatings. Assumed, that in future appear coatings with intelligent properties, capable independently recover after damage and adapt to changing conditions operation.
According to forecasts Global Market Research, market corrosion-resistant coatings will increase by 9% by 2025, what due to growth industrial demand and environmental requirements. Company C already engaged in development such technologies, reducing operational costs by 20%.
Accent also will be made on reduction environmental impact production processes and use renewable resources, what will allow integrate green technologies in sector coatings.
Thus, corrosion-resistant coatings for accessories cable trays remain important area research and development, contributing to increase reliability and efficiency cable systems in diverse conditions operation.
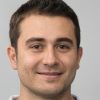
Skateboarder, tattoo addict, fender owner, Swiss design-head and RGD member. Acting at the intersection of minimalism and sustainability to craft experiences that go beyond design. Let’s design a world that’s thoughtful, considered and aesthetically pleasing.
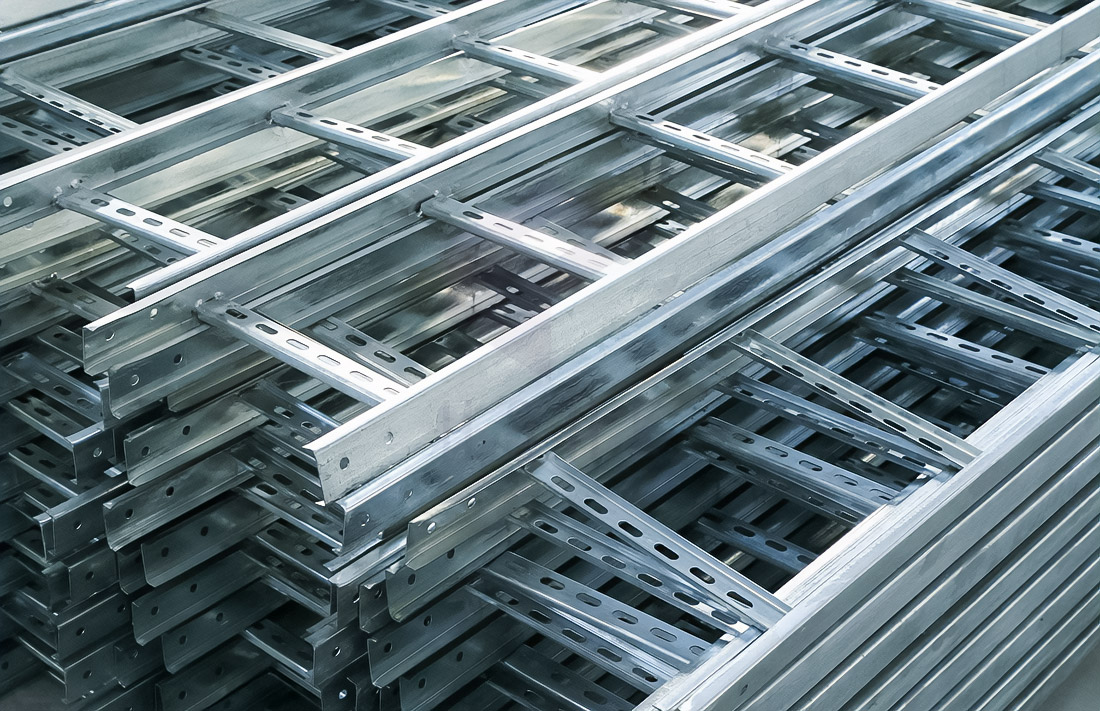
Cable trays and their accessories — this important elements modern cable systems, providing reliable and organized laying wires and cables in buildings and industrial facilities. Trays manufactured from various materials, including steel, aluminum and plastic, and can be presented in form ladder, perforated or solid structures. Accessories, such as connecting elements, fasteners and plugs, play…
![]()